gear up your cae for industry 4.0


additive manufacturing

design flexibility
reduce material wastage


net zero by 2050

" ... slash 45% of greenhouse gas emission by 2030."
how GEARED up are you?
Are you focussing only on the manufacturing aspect?
What about the design?
Design for additive manufacturing

topology optimization


- weight reduction
- material wastage
- costs

- performance
- efficiency
- product life cycle
In applied mathematics,
"Topology optimization is a mathematical technique that seeks to find the optimal distribution of material or structural layout within a design domain, subject to certain constraints, in order to maximize or minimize a specific objective function, often related to performance, cost, or efficiency."
- democratize the state-of-the-art
- enable more efficient engineering designs
- made for engineers, not numéricien
- reduce the product development time
- reduce the design iterations
we
envisage
"a perfect starting point for design engineers"
-
faster computations
-
supercomputing from browser
-
scale compute resources on-demand
-
no more RAM/memory shortage
-
AMD EPYC™ series CPUs upto 480 cores
-
powered by Microsoft Azure

hardware
- efficient parallel MPI code
- curated on state-of-the-art libraries
- scalable on 1000s of processes
- perform large-scale design optimizations
- minimal or no manual postprocessing

software
levels
high-fidelity structural topology optimization cloud suite

-
Aerospace
-
Automobile
-
Mechanical
-
Architecture
levels
high-fidelity structural topology optimization cloud suite
-
state-of-the-art MPI parallelized adaptive refinement
-
enable finer discretization with faster computations
-
reduced error in numerical approximations
-
more accurate computations, more accurate designs
-
smooth and accurate geometries, no manual postprocessing
-
enable faster large-scale designs generated with cloud HPC
-
perfect start to the AM workflow
- Upload part model in STEP format
- Specify support faces
- Specify load faces with their traction loads
- Specify non-design spaces (if any)
- Specify material parameters
- Specify design parameters

GE jet engine bracket
lightweighting


- supports
- loads

GE jet engine bracket

60% weight reduction
GE jet engine bracket

80% weight reduction
alcoa aircraft bracket
lightweighting


- supports
- loads

curved roof supports
Architecture

- supports
- loads


curved roof supports
Architecture

curved roof supports
Architecture

entrance facade of the qatar national convention centre (qncc)
latticing/infills for purely structural parts?
channels
high-fidelity thermo-fluid topology optimization cloud suite
custom cold plates for high heat density power electronics cooling

-
microchannel cooling
-
data center microchip cooling
-
EV power modules, battery cooling
-
high-power electronics cooling
Conventional cold plate channels
Conventional cold plate channels
-
non-uniform temperature distribution/cooling
-
high pressure drop/pump energy requirements
-
low thermal performance, heat transfer
-
localized heating of power electronics
-
Select cold plate layout based on manifold/port locations
-
Specify cold plate, manifold/port dimensions
-
Specify inlet conditions - temperature, velocity
-
Specify fluid, solid region material parameters
-
Specify heat to be dissipated/heat source


-
Improved thermal performance
-
Minimized pressure drop
-
WEIGHT REDUCTION
-
Improved life cycle of cooled electronics
work in progress


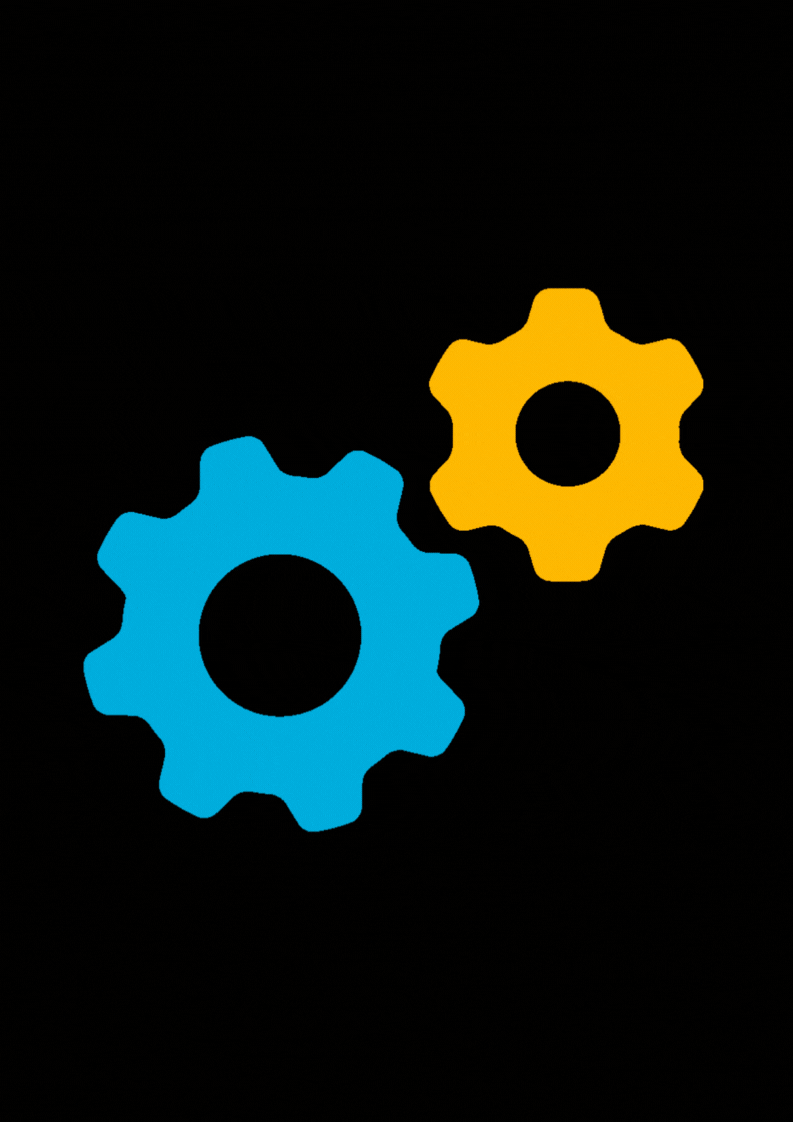
Multiphysics cloud simulation platform
curved roof supports
Architecture
